Process Mining vs Process Modeling: What Differentiates The Two
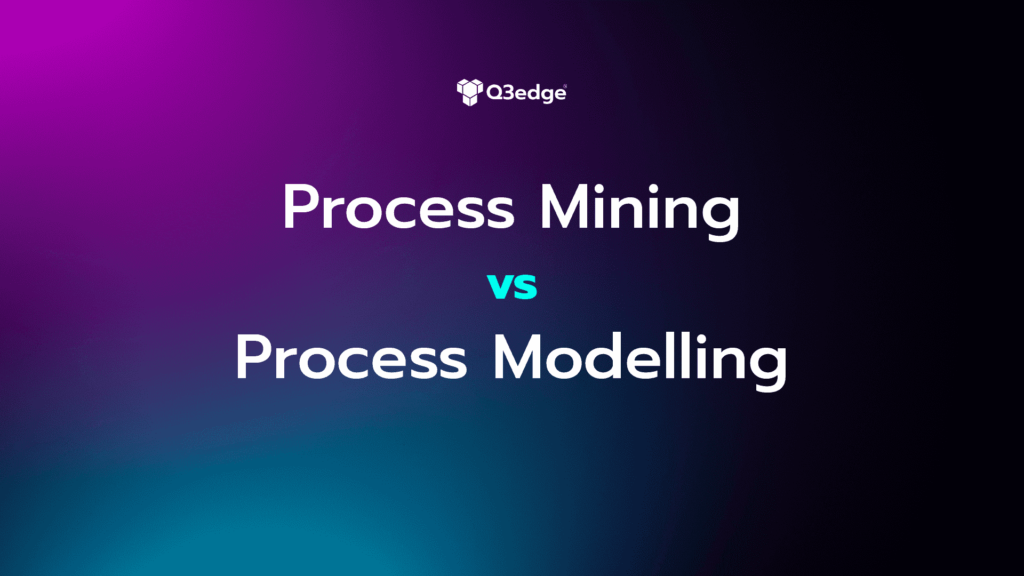
The business environment has become highly dynamic, regardless of the sector. All businesses need to be ready for constant transformation as it allows them to stay at pace with the market needs and trends. It will enable organizations to not only serve market conditions but also match customer expectations as well. So, having a proper strategy for the desired transformation is essential, and this can only happen if one has adequate know-how of the present mode of operation. It is where the world of process mining vs process modeling comes into play.
These two aspects are two sides of one coin and complement each other in the transformational journey of business. If you are thinking about what differentiates them, then we have all the answers for you.
Process Mining vs Process Modeling: Key Drivers of Business Transformation
Process Mining: All You Must Know About It
The Process Mining Advantage
- Objective process visibility – using event data to analyze actual workflows
- Fact-based decision making – Leverage data to plan transformation roadmap
- Early issue detection – Alerts on deviations enable proactive actions
- Continuous monitoring – Track processes dynamically with automated dashboards
Process mining is a technique that analyzes event logs from information systems to discover, monitor, and improve real processes. It helps gain valuable insights into as-is operations through a data-driven analysis of processes. Business process management software automatically records event logs that can be used for process mining.
These event logs contain information about the started and completed activities, including timestamps, resources involved, and other relevant case data. Process mining techniques are then applied to these logs to discover the actual processes that are currently in place within an organization.
Through an unbiased analysis, process mining can reveal inefficiencies, bottlenecks, and improvement opportunities that often remain undiscovered otherwise. It highlights touch points, where current ways of working may need to support evolving customer or market, needs adequately.
For example, process mining of order management systems could identify that a majority of customers need to modify their orders in some way before delivery. However, the existing processes may allow changes only until a certain step in the journey. It leaves room for improving the flexibility of processes to enhance customer experience. Such insights derived from process mining analyses pinpoint exactly where processes need refinement to achieve strategic goals effectively.
Benefits of Process Mining
Some key benefits of leveraging process mining include:
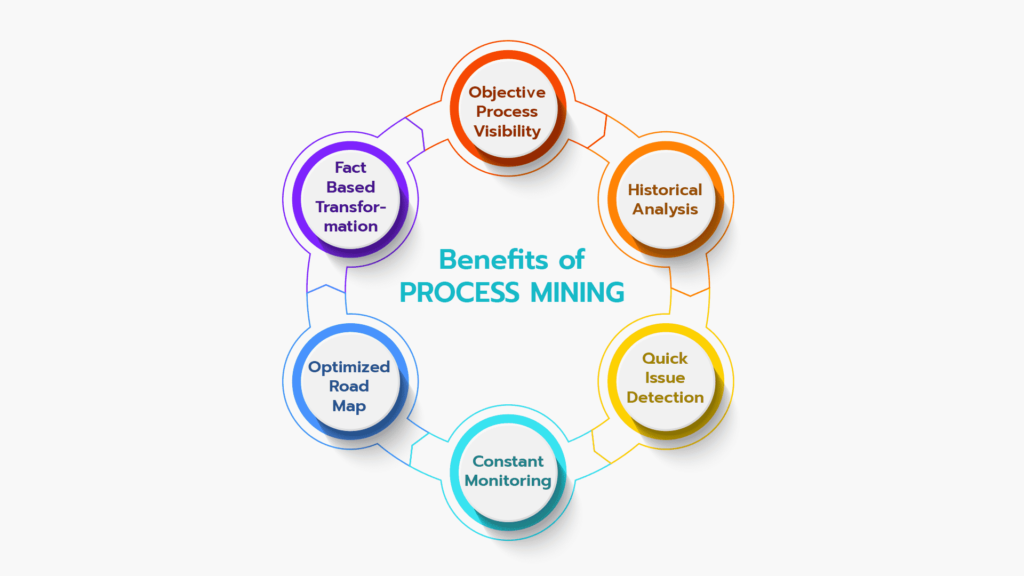
Objective process visibility
Unbiased data-driven insights into actual steps, sequences, performers, and bottlenecks in processes.
Historical analysis
Ability to analyze processes over time to understand variability, drifts, and impact of changes.
Quick issue detection
Alerts whenever processes deviate from acceptable norms.
Constant monitoring
Configure automatic monitoring dashboards to track KPIs continuously.
Optimized road map
Prioritized improvement recommendations based on mined results.
Fact-based transformation
Hard data support a solid basis for planning process changes.
Process Modeling: All You Must Know About It
Process modeling refers to the practice of visually documenting organizational processes. It involves creating simplified step-by-step representations of workflows, activities, roles, and dependencies that reflect how an organization ideally wants certain processes to operate. Process models streamline processes by eliminating non-value-adding activities, improving handoffs, and setting benchmarks for efficient execution.
Process modeling plays a pivotal role in clearly communicating changes sought via transformation initiatives. It sets the bar for desired ways of working in the transformed state. During process modeling, insights from process mining analyses are leveraged to ideate changes addressing previously discovered inefficiencies or gaps in existing processes.
Process models thus created serve as blueprints for implementation, helping align expectations across functions. They aid in planning resource requirements, timelines, and change management activities involved in rolling out transformations successfully.
Benefits of Process Modeling
Some key benefits organizations reap through process modeling include the following:
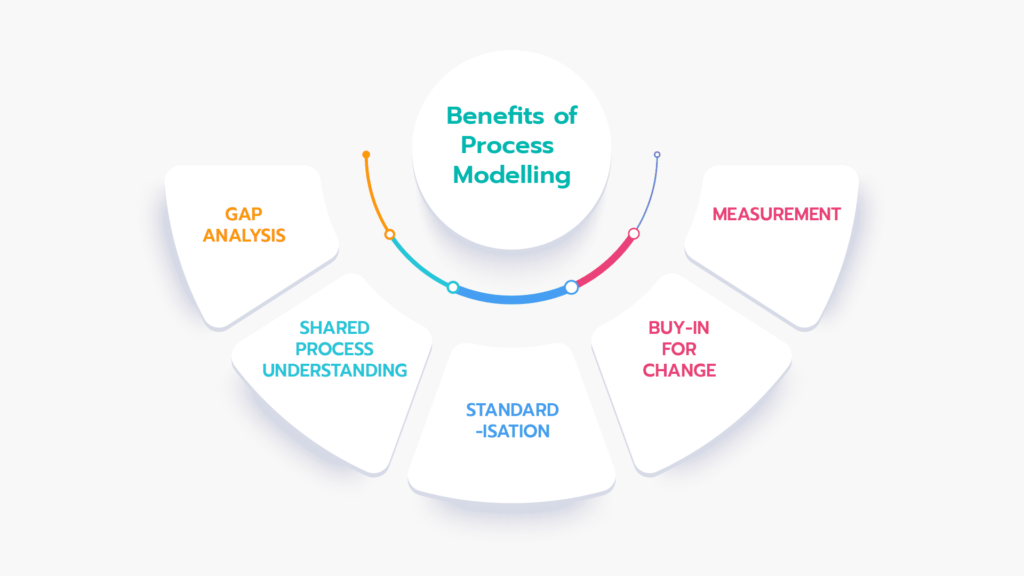
Gap analysis
Identify deviations in current versus desired processes uncovered via mining.
Shared process understanding
Visual depictions facilitate understanding processes holistically across functions.
Standardization
Enable consistent execution of streamlined processes once enacted.
Buy-in for change
Communicate the need for transformation by contrasting sub optimal processes.
Measurement
Set targets for automation, cycle times, compliance, and KPIs.
Having discussed the individual aspects, let us now delve deeper into how process mining and modeling work in tandem to fuel effective transformation.
Process Mining: The Starting Point
As established earlier, process mining provides an objective view into actual ways of working using data from event logs. It presents often undiscovered realities about existing processes instead of making assumptions. Mining analysis pinpoints specific aspects needing improvement, keeping strategic goals in mind.
For instance, a manufacturing company wants to reduce order fulfillment times by 25%. Process mining of order management systems shows numerous manual reviews and approvals, causing delays. It suggests automating standardized checks while retaining strategic reviews. It offers a data-backed proposal to management for discussion and creativity.
Process modeling then begins by considering such insights from mining. With a thorough understanding of current processes’ strengths and limitations, modeling teams are equipped to ideate holistic changed processes. They eliminate non-value-adding steps while retaining crucial differentiators. Modeling also helps map process inter dependencies critical for planning change implementation.
Process Modeling: Realizing Transformation Goals
The process model depicting the envisioned transformed way of working acts as a clear roadmap for stakeholders. It aligns expectations by communicating precisely what change will entail across functions and roles. Resources can then be allocated for development and training required in the new workflows.
For our manufacturing example, the new process model highlights automated checks and approvals. It estimates the effort required to integrate these into order systems and user learning. Timelines are also set factoring system and organizational readiness. Regular reviews using mining keep tabs on progress tracking benefits realization. Refinements are made wherever needed, collaborating cross-functionally.
Final Thoughts: Institutionalizing Process Changes
Sustaining transformations requires ongoing efforts like monitoring for drifts back to legacy behaviors. Process mining plays a crucial role here by enabling continuous oversight of new processes. It scans for deviations from expected patterns, highlighting issues early on. Automated analytics also track benefits, prompting course corrections when targets are unmet.
Regular process mining and modeling cycles thus fuel continuous improvement cultures. They maintain strategic alignment through fact-based prioritization of opportunities. Most importantly, bringing various functions together in this quest for operational excellence breaks silos, paving the path for truly connected enterprises.