What Process Mining Is and Why Companies Should Do It
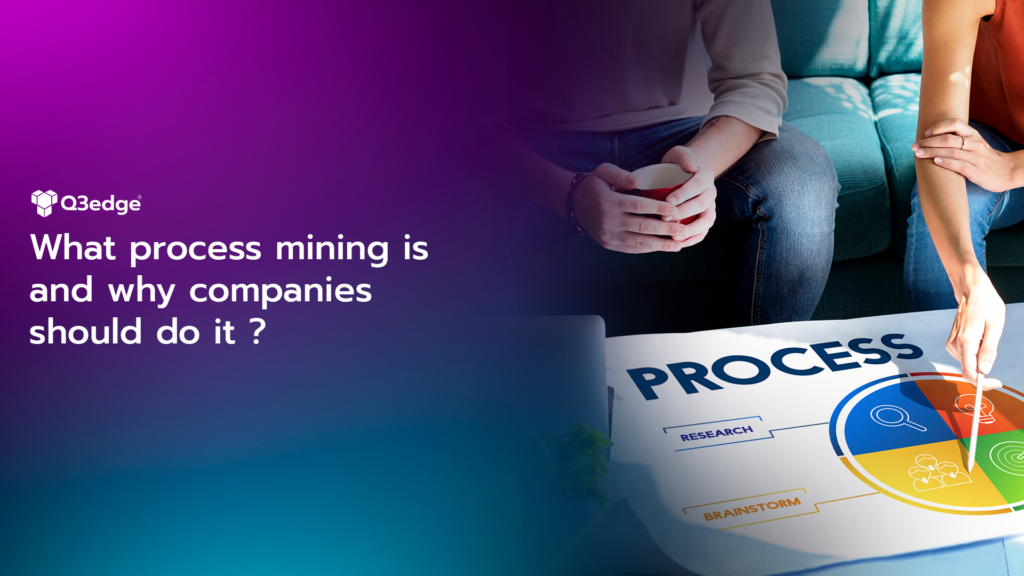
For many years, businesses have faced some basic but tough challenges when it comes to managing and improving how their work gets done — something known as business process management. In our 40 years of working in this field, we’ve noticed that two major issues often make companies put process improvement on the back burner. However, there’s a new and promising technology called process mining that can help solve both of these problems. It has the power to breathe new life into process management, especially in companies where it hasn’t been a priority for a long time.
One common issue in business process reengineering is figuring out how a process is currently being done — also called the “current state” or “as-is” process. Many organizations focus only on the improved version they want in the future, known as the “to-be” process, and don’t pay much attention to how things are working right now. But if you don’t fully understand the current process, it’s hard to know if making changes is even worth it, where the problems are, or how different teams might be doing the same task in different ways. Because of this, some companies either skip analyzing the current process, rush through it with shortcuts, or spend a lot of money hiring consultants to do it for them.
Companies that choose to improve their processes step by step often end up spending too much time trying to understand how things are currently being done (the “as-is” process). They usually gather this information by talking to employees and using sticky notes to map everything out. But this method can feel more like personal opinions than solid facts, which makes business leaders question how reliable the results really are — and understandably so.
Another big challenge in managing business processes is that they’re not well connected to the company’s main software systems. Some large systems like SAP are built to support certain processes (like taking orders or managing payments), but it’s still hard to see how these processes actually work in real life just by looking at the system.
There are tools like Microsoft Visio or Software AG’s Aris that help design process diagrams, but if you want to check how well a process is working on a daily basis, you usually have to collect and combine data manually — and that’s not easy. Plus, many popular improvement methods, like Lean and Six Sigma, don’t really focus on using technology to support or manage these processes.
Introducing Process Mining
Process mining is a new way to solve the common problems businesses face in managing their processes. For years, it was mainly something researchers talked about, especially a Dutch computer scientist named Wil van der Alst. It wasn’t used much in the real world—until 2011, when a company called Celonis was started in Munich, Germany.
Celonis made process mining useful for businesses. Today, they’ve built four powerful versions of their software. They work closely with big companies like SAP (which even sells Celonis software), and their tool can pull data not just from SAP but also from other popular systems like Oracle, Salesforce, and ServiceNow—basically, from almost any business software using APIs.
Suddenly, process mining is getting a lot of attention. In 2018, a well-known research company called Gartner released a report explaining how businesses can use process mining and reviewed the companies offering these tools.
They found more than a dozen companies making process mining software, most of them located in Europe. Celonis was named the top company in this field. Another tool called Fluxicon, from the Netherlands, is known for its deep analysis features, and QPR Software from Finland is one of the oldest and most complete tools available.
Since many of these companies are European, it shows that process mining is more advanced in Europe for now. However, some U.S. companies have also started using it and are seeing its benefits.
Visit Here: Malcom Baldrige Performance Excellence Program.
Process mining software helps companies easily collect information from their business systems and shows clear, data-based insights into how their important processes are really working.
As tasks are done—like receiving an order, delivering a product, or making a payment—the software automatically records these actions as event logs. These logs help companies see what’s actually happening behind the scenes: who did what, how long it took, and where things went off track.
The software also provides performance metrics, so businesses can clearly see which steps need attention. On top of that, AI can identify problem areas—like showing that new customer credit checks often slow everything down. This helps businesses know exactly where and how to improve.
Choosing the right area to use process mining is very important. It works best for business processes that are already handled by some kind of computer system, but still have parts done manually — like reviews or approvals done through emails or calls.
Experts in process improvement know that fixing complex processes isn’t just about looking at data — there’s more to it. As Jaakko Riihinen from QPR Software explained, process mining depends on the data it can collect from system logs. That means it can only give insights based on the information that’s already being tracked.
Even with some limits, process mining is a game-changer for people who are responsible for managing or improving how a business runs. It takes away the hard work of manually figuring out how a process currently works — the software does that automatically.
Even if you’re not looking at the whole process, you can still see what’s happening in your own part of the work and fix any issues. If your company uses software systems (like SAP, Oracle, etc.) to run important business tasks — which most large companies do — then it’s definitely worth looking into process mining. It can help you work smarter and solve problems faster.
Visit Here: Business Process Architecture and Modelling.
Process Mining at Chemours
Chemours is a global chemistry company that was formed in 2015 when DuPont separated its Performance Chemicals division. This division included products like titanium technologies, fluoroproducts, and chemical solutions. Now, Chemours operates as an independent company worth $6 billion, with 7,000 employees, 26 manufacturing sites, and around 4,000 customers spread across more than 130 countries.
When Chemours became its own company, it inherited its business processes and an old ERP system from DuPont, along with a strong focus on improving these processes. As part of their efforts to make the company more efficient and flexible, they became interested in process mining. Chemours bought Celonis software, and the first process they decided to focus on with process mining was the order-to-cash (O2C) process. Dean Meyer, the Chief Information Officer (CIO), led the overall transformation, while Mark Newman, the Chief Financial Officer (CFO), supported the O2C project. Sung Lee, the Director of Business Process Transformation, manages the process mining project and highlighted that the company’s leadership has been supportive from the start, which has been key to its success.
Before starting the process mining project, no one at Chemours really knew how the entire order-to-cash (O2C) process was working because people usually only see their own part of the process. It took four months of process mining to reveal how the actual process was running, which was different from what the ERP system documentation showed. The process mining uncovered some major problems, like customers being unnecessarily put on credit hold. This happened to some important customers just to allow manual steps in the O2C process.
While the full benefits of process mining for Chemours’ order-to-cash (O2C) process are still being worked on, many problems have been identified. Over 40 projects are now underway to fix these issues and make the process simpler, more unified, and automated. Sung Lee mentioned that process mining has helped teams better understand their roles and collaborate more across departments. They now have a clear view of the entire process, including where things deviate from the normal flow, based on different businesses and product lines. In 2019, Chemours plans to use process mining for another process called source-to-pay (S2P). The company has also tested combining process mining with robotic process automation (RPA), aiming to make work more focused on customer interaction and improve business performance analysis.
Also Read This: What is a Business Process – Definition, Types, Characteristics, Importance, and Lifecycle.
Process Mining at Q3edge Consulting
Q3edge Consulting is a leading provider of business process management and automation services, helping businesses improve efficiency and streamline operations. With a strong focus on customer satisfaction and operational excellence, Q3edge has built a reputation for driving continuous improvement through advanced technologies. Over the years, the company has embraced various methodologies, including Lean Six Sigma and Agile, to enhance its services and deliver measurable results for clients across different industries.
The Business Process Management (BPM) department at Q3edge is responsible for deploying process mining services, with a dedicated team managing the efforts across various client projects. The company utilizes advanced process mining software to analyze operational processes and uncover inefficiencies. This service is designed to provide deeper insights into the performance of key business processes such as order-to-cash, procurement, and customer support, improving workflow transparency and boosting overall productivity.
One of the main advantages of process mining at Q3edge is that it offers greater visibility into the workflow, enabling companies to identify non-value-added tasks and eliminate manual reporting efforts. By uncovering inefficiencies in business operations, process mining helps Q3edge’s clients reduce delays, lower operational costs, and make data-driven decisions that lead to continuous improvements.
According to the Director of Process Mining at Q3edge, the transparency offered by process mining has significantly improved internal benchmarking and cross-department collaboration. This allows the company to identify best practices across various business units, leading to greater efficiency and improved performance.
For example, many Q3edge clients assumed that processes like procurement or customer invoicing should be straightforward. However, after implementing process mining, unexpected variations and inefficiencies were identified, allowing Q3edge to refine these processes and provide clients with a clearer path to improvement.
Looking ahead, Q3edge plans to integrate process mining with other advanced technologies such as robotic process automation (RPA) and artificial intelligence (AI). This integration will further enhance the ability to automate routine tasks, optimize workflows, and drive even greater value for clients across different industries.
Process mining might not be suitable for every business. It’s especially helpful for large companies that focus on quality and want to compare their performance across different parts of the business. If a company doesn’t usually focus on improving its processes, then process mining might not be the best fit for them.
Process Mining and Other Technologies
Process mining is great for understanding how well business processes are working, spotting areas that need improvement, and measuring the results after making changes. It works really well with other tools, like robotic process automation (RPA). First, process mining can find the best places to use automation (or “bots”), and then it helps track how much those bots improve things.
Process mining shows a clear and data-backed view of how business processes are performing, making it easy for senior leaders to spot problems and opportunities. It helps push a company towards making decisions based on solid data. Some companies have already figured out the best ways to use process mining with robotic automation (RPA) to improve things. In the future, we expect to see more solutions that combine process mining, RPA, and machine learning to work even better together.