How to improve Overall Equipment Effectiveness (OEE)?
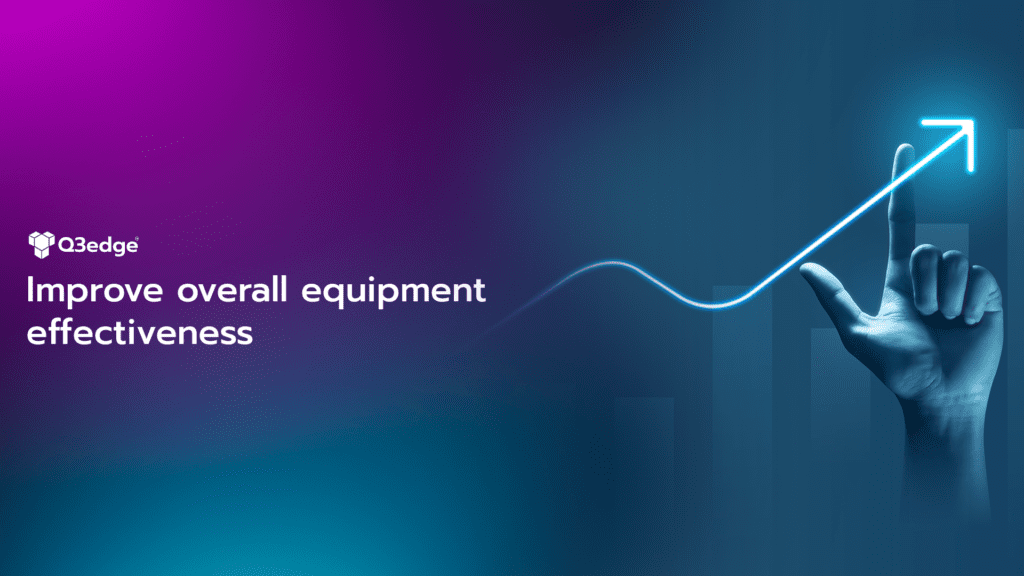
In a manufacturing unit filled with a diverse equipment, it is difficult to identify the faults or defects in the machinery. Hence, to make the task of operators easy, OEE was developed. It is a form of mathematical calculation that helps analyze a machine’s defects and find ways to improvise its functioning. OEE is only a measure to gauge the functioning of machines, but you must find ways to improve overall equipment effectiveness. An increase in the OEE score leads to an enhancement in the functioning of machines in the manufacturing unit.
What is Overall Equipment Effectiveness?
Before knowing ways to improve OEE, it is essential to understand it briefly.
Overall Equipment Effectiveness (OEE) is a metric that measures the functioning of a running manufacturing unit compared to its full potential.
To simplify, OEE measures the percentage of productive manufacturing time.
The two different methods to calculate OEE are,
1 Simple Calculation
- It is the easiest way to calculate Overall Equipment Effectiveness.
- It is the ratio of full production time to the planned production time.
The formula is,
OEE= (Good Count * Ideal Cycle Time) / Planned Production Time.
2 Preferred Calculation
- This method has 3 essential attributes. They are Availability, Quality, and Performance.
- It is the most preferred way of OEE calculation because it denotes the problem in the manufacturing and gives a clear scope to improve it.
The formula is,
OEE= Availability * Performance * Quality.
Different Ways to improve Overall Equipment Effectiveness
There are different ways to improve the OEE score, which can either be done by incorporating simple changes or by adopting automation into the practice; a few of the methods are:
1. Eliminating the Six Big Losses First
It is time to address the elephant in the room; the main purpose of OEE is to identify the six big losses.
• The six big losses that govern the overall equipment effectiveness score are- Equipment Failure, Adjustments and Setup, Minor Stops, Slow Cycles, Process Defects, and Reduced Yield.
• The above Six Big Losses are the primary reasons that cause the overall equipment effectiveness score to diminish; however, when these losses are taken under control, the score automatically jumps to a greater number.
• The Six Big Losses arise from improper supervision, management, untimely reporting of the initial problems in the equipment, unskilled labor, and lack of training and awareness.
For Example, if the supervisor and operator monitor the machine thoroughly before starting to work, they can recognize defects in the machine and eliminate the first big loss, Equipment Failure.
• Re-growth in OEE directly results from the six big losses; hence, the first strategy to improve the score is to address the six big losses and find solutions.
2. Examining All Production Stops
• Production stops are one area where the supervisors and operators can take advantage.
• Usually, production stops are inevitable in a manufacturing unit due to downtime, system maintenance, cleaning, shift change, and many other reasons.
• The manufacturers need to design a system where the operators explain every production stop, identify the root cause, and discuss it with managers and HODs.
• The examination process will make them more aware of the situation and reduce work leniency.
• It will also reduce unnecessary production stops or downtime, increasing the overall equipment effectiveness score.
3. Production Planning and Plant Layout
• The production planning should assist and ease the manufacturing process in a plant.
• The plant layout helps to relocate spaces and allocate equipment so that it minimizes the operating costs.
• The layout should enhance the productivity of the manufacturing unit.
• Today, plant layout design has taken a step toward conserving electricity. It is known as Green Manufacturing. The benefits of energy management are enormous, but the most evident ones are reduced operational costs and less hazardous.
• Systematic Layout Planning (SLP) and Lean Tools are employed to design a Green Manufacturing Unit.
4. Induce Preventive Measures
• The risk of errors and defects cannot be reduced to zero in any manufacturing unit.
• Hence, it is important to induce preventive measures to act as a Plan B for the manufacturing unit.
• The first approach is to identify the defects in equipment at the early stages and repair them, which will reduce the excess costs in the future for bigger damage.
• The second approach is to have timely maintenance checks for all the equipment present in the manufacturing unit. It reduces a lot of burdens and keeps the machines new always.
• It is crucial to know the root cause of a problem. Machines can have several technical problems, of which some can be dealt with immediately, which helps the manufacturing process.
5. Training and Workshops for Operators
• Every ground-level Operator and managerial position Supervisors recruited to handle the manufacturing unit should be given proper training.
• A proper training will ensure adequate knowledge of the equipment, which will assist them in meticulously monitoring and maintaining the plant.
• Apart from training, the manufacturers should conduct frequent workshops to impart knowledge on current trends and new equipment and technology.
• Ultimately, Knowledge is bliss, and it is the only pathway out of ignorance. And knowledge can also help increase overall equipment effectiveness scores.
6.Practicing Cross-Functional Daily Reviews and Discussion sessions
• It is always beneficial to involve more minds to improve a process or functioning; the same applies to the functioning of a manufacturing unit.
• Cultivate a team that can have healthy talks daily, review each other’s performances, and participates in discussion sessions which provides room for improvement for everyone.
• When different people from diverse teams meet together to discuss the functioning of the manufacturing unit, there will be multiple opinions flowing in from different people. The different opinions can be analyzed and put into use for the better functioning of the workplace.
7. Incorporating a Digital Approach
• The approach involves eliminating manual intervention in calculating OEE and assigning a digital champion to calculate the score.
• The benefit of doing so is that sometimes the OEE score doesn’t match the attributes like Availability, quality, and performance. All the attributes look perfect, but the score is low; hence, it becomes challenging to detect the error.
• In such cases, a digital champion can calculate the correct score and save the company time.
• Machine vision is another way to sustain a digital approach. Machine vision is an image-based process to mechanically examine parts of a manufacturing process and ensure proper functioning.
• It uses machine sensors that can alert when there are errors or defects, hence verifying the processes with ease—ultimately improving the OEE score.
•Digital Automation is a game-changer in manufacturing units.
• Most manufacturing units use the traditional approach of appointing different supervisors in different processes for supervision, who are also responsible for collecting related data concerning the process and the machine and reporting it to the higher authorities.
• This hierarchy, if well-maintained, works very well, but if this is disrupted for some reason, the burden falls on the manufacturing unit. Hence, data processing and reporting automation can be adopted by manufacturers to eliminate the risk of disruption.
• Automating helps in improving overall equipment effectiveness to a very stable and good score with ease.
8. Introducing Real-Time Display of OEE
• When the OEE score can be constantly visualized on the shop floor, it’s hard to stop thinking about improving it.
• It is like showing a mirror to yourself, which will result in a great output as you will always be on the go to improve the score.
• Real-Time Display acts as a catalyst for people in supervision and maintenance sections.
• Without any further doubt, it improves the OEE score and gives an instant boost in productivity.
Conclusion
Valuing your investments is the primary duty of any person. Equipment is a valuable investment for a manufacturer. OEE score is an indirect measure of the defect in either the machine or the process.
Hence, there is no harm in investing in improving overall equipment effectiveness. However, the manufacturer should always remember, along with investing in the equipment and processes, that he is also increasing his manufacturing business’s shelf life.